由于大口径闸阀阀体容纳闸板的内腔通常为扁圆形或接近椭圆形的异形容器,所以它的变形较大,如大圆和小圆的倒角处会出现应力集中。针对这些情形,通过采用在阀体内腔外围加筋的方案来解决这些问题。本文以阀体最大等效应力为目标函数,加强筋的结构尺寸为设计变量,采用有限元软件ANSYS—Workbench的DX模块中的确定性优化方怯对筋的结构尺寸进行优化,使筋的结构分布更合理,使得整个阀体变形协调,最大等效应力显著下降。
1.阀体有限元模型建立及优化分析过程
1.1 三维参数化模型的建立
阀体的参数化模型应该能准确反映结构的实际状况,即其形状、边界条件和载荷与实际情况要保持一致,同时在保证计算精度的情况下,模型应尽可能简化。因此在建模过程中对阀体的一些不影响总体性能的特征进行了简化处理,忽略了一些不必要的倒角,最后的计算模型。
阀体的材料为WCB,材料特性为:杨氏弹性模量E=206GPa,泊松比μ=O.25,材料的许用应力[σ]=120.69MPa。
以阀体为分析对象,模拟阀体在水压试验时的受力状况。阀体在水压试验时,在阀体进出口两端法兰施加固定约束,中法兰施加y方向约束;根据阀门水压试验要求,按设计压力的1.5倍在阀体内表面施加7.5MPa压力作为计算压力。
依据图纸建立大口径闸阀,进行有限元单元划分,有限元网格单元的类型为10节点四面体,单元基本大小为30mm,单元总数目为30383个。
1.2 计算结果
经计算机求解后,得到由第三强度理论为基础的阀体等效应力。阀体最大等效应力为151.65MPa,最大等效应力超出材料许用应力范围,在阀体中腔有明显的应力集中现象;阀体最大位移为0.14735mm,也出现在阀体中腔处。原因是此处形状发生突变,并且截面为近似椭圆体形状,受力状况不好。因此,在阀体中腔外部加加强筋,以此增加阀体强度,降低阀体最大等效应力,位移变形量,使阀体变形协调。
1.3 加筋后的模型
根据闸阀中腔外壁的结构尺寸加三筋,三筋中靠近中法兰的为第一条筋,往下依次为第二条筋和第三条筋,第一条筋处中腔外壁形状接近圆形,筋设计成圆形;第二条筋和第三条筋设计成近似椭圆形。
加强筋有沿厚度方向和垂直于厚度的径向方向。
在径向方向,近似椭圆形结构尺寸主要由小圆半径R1,大圆半径R2,过渡倒角R6决定。
圆形结构尺寸由圆半径R决定。分别以:
第一条筋的圆半径r1=314.4mm为第一个参数;
第二条筋的小圆半径r2=314.4mm,大圆半径r3=1275mm,过渡倒角r4=200mm为第二,三,四个参数;
第三条筋的小圆半径r5=314.4mm,大圆半径r6=1230mm,过渡导角r7=100mm为第五,六,七个参数。
在厚度方向,分别以:
第一条筋的厚度h1=30mm为第八个参数;
第二条筋的厚度h2=30mm为第九个参数;
第三条筋的厚度,h3=30mm为第十个参数。
1.4 加筋后的计算结果
加筋后,进行力学分析,阀体最大等效应力下降为100.23MPa。阀体中腔处最大位移减小为0.086868mm。
加筋后,阀的质量由原来的616.3kg增加到654.4kg。筋的质量增加了38.1kg增加了6.18个百分点.阀体最大等效应力由151.65MPa下降为l00.23MPa,下降了33.9个百分点。并且应力分布更加均匀。阀体中腔处的位移也显著下降。
但这还不是最理想结果,本文研究的大口径闸阀阀体中腔为连续渐变的椭圆结构,其受力十分复杂,在其外部加的加强筋结构参数也多。我们不能盲目通过增加筋的厚度和横向尺寸,来降低阀体的应力,这样会增加阀体质量和成本;除此之外,阀体还受铸造工艺。安装要求的限制。因此,我们也不能盲目增加加强筋,有必要对加强筋的结构进行优化。即在一定的设计范围内。寻求结构的最优解。因为合理的加强筋结构质量分布更能提高阀体强度与刚度。
2.阀体加强筋结构优化
2.1 影响阗体强度的加强筋结构参数化及其优化
以阀体质量约束条件下阀体最大等效应力更小化为目标函数,以阀体加强筋结构的尺寸作为设计变量,对阀体加强筋结构进行优化。本文仅以加强筋的六个主要参数来研究它们对阀体最大等效应力影响。
对加强筋r1,r3,r6,h1,h2,h3的进行参数化,分别以这些参数为优化变量进行优化。
(1)优化目标:阀体最大等效应力。
(2)加强筋结构参数化
第一条筋的半径ds_R1为设计变量,初值为314.4mm,根据螺栓安装要求确定优化范围为290~330/mm;
第二条筋的大圆半径ds_R2为设计变量,初值为1275mm,根据阀安装要求确定优化范围为1250~1310/mm;
第三条筋的大圆半径ds_R3为设计变量,初值为1230mm,根据阀安装要求确定优化范围为1210~1270/mm;
第一条筋的一半厚度ds_FD1为设计变量,初值为15mm,根据螺栓安装要求确定优化范围为7~15/mm;
第二条筋的一半厚度ds_FD2为设计变量,初值为15mm,根据铸造要求确定优化范围为7~20/mm;
第三条筋的一半厚度ds_FD3为设计变量,初值为15mm,根据铸造要求确定优化范围为7~20/mm。
(3)优化方法:采用一阶优化方法,即通过对目标函数添加罚函数将有约束的多变量非线性规划问题变成无约束的非线性规划问题,以因变量对设计变量的偏导数来决定搜索方向,自动运行优化程序,在优化的每一次循环中都对模型重新划分网格,完成优化分析。
(4)参数的灵敏度分析
由图10可知,参数的灵敏度显然不同,FD3即第三条加强筋厚度的灵敏度最高为O.1770,R1即第一条加强筋半径的灵敏度最低为-0.0128。同时这些参数的灵敏度符号不同,有正负之分,正号表示随参数的增加,阀体最大等效应力在减小,负号表示随参数的增加,阀体最大等效应力在增加。在本文指定的设计参数中,阀体第三条加强筋厚度对阀体最大应力的影响所占的比重最大;其次为第二条加强筋厚度和第二、三条加强筋大圆半径;第一条加强筋的厚度和半径两个参数对阀体最大等效应力的影响比重最小。
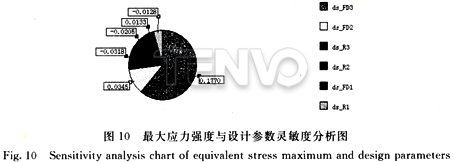
(5)参数对阀体最大等效应力的影响
第一条加强筋设计变量ds_FD1接近11mm时,阀体最大等效应力最大,当偏离这个值时,应力减小很快。如图11所示。
第二条加强筋设计变量ds_FD2逐渐增大时阀体最大等效应力逐渐减小。如图12所示。
第三条加强筋设计变量ds_FD3接近16mm时,阀体最大等效应力最小,当偏离这个值时,应力上升很快。如图13所示。
第一条加强筋设汁变量ds_R1接近305mm时,阀体最大等效应力最大,当偏离这个值时,应力减小很快。如图14所示。第二、三条加强筋与第一条加强筋情形相似。
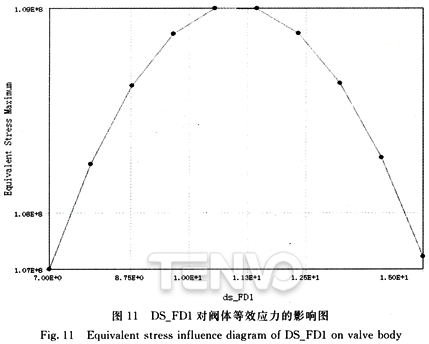
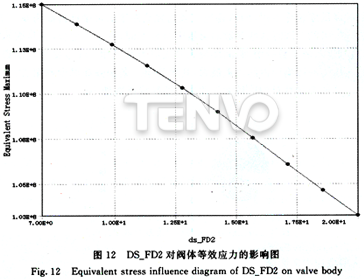
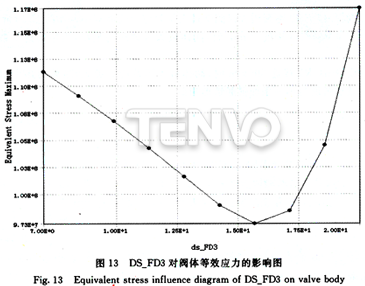
以上是单个参数对阀体最大等效应力的影响,下面是两个组合参数对阀体最大等效应力的影响即应力强度设计空间,如图15所示。
经优化后得到设计变量的优化值:
第一条筋的半径R1,由初值为314.4mm变为324.55mm;
第二条筋的大圆半径R2,由初值为1275mm变为1301mm;
第三条筋的大圆半径R3,由初值为1230mm变为1258.5mm;
第一条筋的一半厚度FDl,由初值为15mm变为8.9261mm;
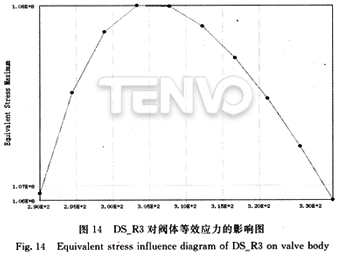
第二条筋的一半厚度FD2,由初值为15mm变为10.458mm;
第三条筋的一半厚度FD3,由初值为15mm变为17.946mm;
由此,我们求得在一定的设计范围内,加强筋结构合理分布的最优解。
优化后第一、二条筋的厚度减小,第三条筋的厚度增加;第一条筋的半径和第二、三条筋的大圆半径都有所增大。
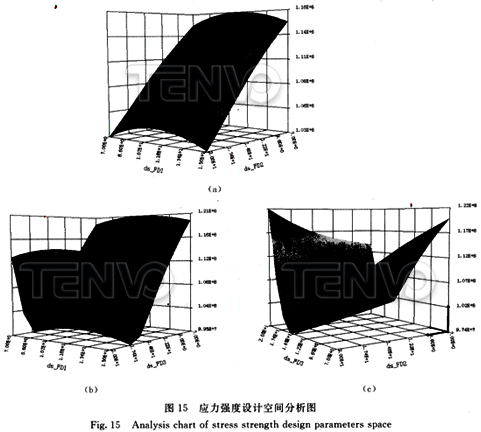
2.2 结构优化后计算结果
优化后的模型进行对有限元分析,材料、网格划分、约束与载荷同改进前相同。
进行优化以后,阀的由原来的质量616.3Kg增加到660.9Kg,筋的质量增加了44.6Kg增加了7.2个百分点,阀体最大等效应力由151.65MPa下降为97.33MPa,下降了35.82个百分点;阀体中腔处最大位移减小为O.082023mm。加强筋优化前后结果比较,见表1。
3.结论
(1)阀体进行加强筋设计后,其阀体强度得到了改善,改进后的阀体等效应力最大值下降了33.9%;阀体中腔处最大位移减小。
(2)利用确定性优化方法优化筋的结构尺寸后,使加强筋结构更合理,阀体最大等效应力更显著下降,下降35.82%:且应力分布更均匀;阀体中腔处最大位移减小,阀体变形更加协调,密封性能得到很大改善。
(3)利用有限元软件ANSYS优化分析模块对大口径闸阀阀体进行结构的优化,大大缩短阀门设计周期,提高设计效率,使阀体结构设计合理。
上海减压阀-天沃,与您资料共享!