1.概述
蒸汽是一种工业领域重要的二次能源,蒸汽系统也是能源消耗的主要领域,我国产煤量的三分之一用于该系统。蒸汽疏水阀则是保障蒸汽系统正常工作、节约能源的重要自力式控制类阀门。随着科技的发展、工业规模的不断扩大,工业生产呈现大容量、高参数、高效低耗的趋势,对蒸汽疏水阀节能效率要求愈来愈高的同时,对排量要求愈来愈大。如在大乙烯、大型化工装置等工艺流程合需要排量50~160T/h的蒸汽疏水阀。目前节能型疏水阀:机械型疏水阀关键元件——浮球、浮筒无法满足大口径时介质力的要求;热静力型疏水阀关键元件——双金属热动力元件单凭多组叠加;液体膨胀式单凭热动力元件体积的增大也无法满足大口径时介质力的要求。
国际上超大排量先导式疏水阀技术一直被西方少数几家大公司垄断。国产只有仿制自由浮球+活塞的先导式疏水阀产品,没有热静力+活塞主阀产品。国内在适合大排量热静力疏水阀的场合仍然需要选用价格高昂的进口产品或采用多组疏水阀组合的落后设计。常见的热静力蒸汽疏水阀主要有双金属型、波纹管型(液体、饱和蒸汽压力两种)、膜盒型和温敏蜡型等。双金属热动力元件是一种技术较为成熟的热动力元件,主要优点在于可适用温度高、结构简单、安全性高、工作稳定,可用于多种介质的温控场合。因此开发超大排量双金属先导可调式疏水阀,满足国内市场以及重大成套装备主要附件国产化对过冷或者过热超大排量蒸汽疏水阀的需求,具有良好的应用前景、经济效益和重大的现实意义。本文对超大排量双金属先导可调式疏水阀的基本原理、结构设计以及主阀导阀关键部件的设计进行了具体研究与探讨。
2.整体结构设计
2.1 整体结构设计
超大排量双金属可调先导式疏水阀是将圆盘双金属疏水阀与大排量截止阀进行了有机的组合,采用先导式结构,通过小阀对大阀的控制,实现了对凝结水超大排量的控制;采用优化设计原理,通过活塞泄压小孔形成气垫、平衡弹簧等的优化组合,实现了避免关闭过快而造成高噪声和引起管路振动甚至水击以及有效延长密封面的寿命。
其结构主要由主阀和先导阀两部分组成(结构简图如图1所示),主阀采用的是活塞与阀芯的一体化结构,导阀采用的是圆盘双金属可调式结构。通过导阀带动主阀工作,使其具有超大排量,实现排水温度可调的功能。
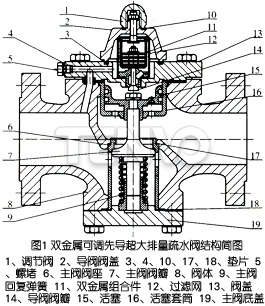
2.2 基本工作原理
超大排量双金属可调先导式疏水阀就是以温敏双金属热动力元件组合件11作为导阀来控制主阀,当阀腔内充满蒸汽时,双金属组合件处在高温环境中而膨胀,使导阀关闭,主阀则由于介质力和弹簧力的共同作用也处于关闭状态,从而起到了阻止蒸汽排出的作用。当阀腔内充满的是冷空气时,热动力元件11则收缩使导阀打开,冷空气就可以经由导阀、活塞15上的小孔而排出,从而起到排空气的作用。当阀腔内流人的是冷凝水时,由于冷凝水的温度低于双金属热动力元件组合件11的动作温度,导阀会打开排水,冷凝水通过导阀阀座孔流入主阀活塞6上腔,由于活塞的截面积远大于主阀阀芯的截面积,活塞与主阀阀芯组件受力合力向下,则主阀打开排水。排水结束时高温蒸汽进入导阀,导阀关闭。在活塞15上设计有泄压缓冲小孔,主阀关闭时,活塞上腔的压力不会迅速释放,即主阀不会迅速关闭,从而避免了主阀阀芯与阀座的猛烈撞击,提高了密封面的使用寿命、有效地防止了主阀关闭过速引起管路振动。
3.先导阀关键技术研究与设计
3.1 双金属组件热动力元件受力分析
3.1.1 建立热推力F与挠度f的数学模型形公式也可用于一般非纯弯曲)。则如图2所示双金属片产生了一定的弯曲变形,设中心处垂直方向上的变形量f与任一点x处的弯矩与挠度的关系为:
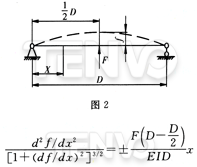
式中:D——双金属片外径,m;
d——双金属片内径,m;
E——双金属片的弹性模量,Pa;
I——双金属片截面的极惯性矩,m4;
F——一片双金属片产生的热推力,N;
f——双金属片中心处垂直方向上的变形量,m;
x——双金属片上任一点到其边缘的距离,m。
由于df/dx的值远小于1,略去后积分并令x=D/2得:

对于导阀中图3所示的环形双金属片,有:
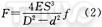
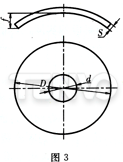
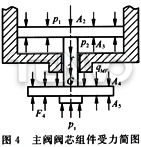
3.1.2计算热推力
由比弯曲关系式:
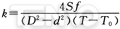
将上式代人式(2)中得:
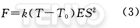
则一组金属片产生的热推力为:

除去凝结水作用在金属片上的压力后的热推力为:

则n组金属片的热推力为:

式中:Po——进口压力,Pa;
k——比弯曲,℃-1;
T——双金属片变形后的温度,℃;
T0——双金属片开始变形时的温度,℃;
n——双金属片组的个数。
3.1.3双金属片导阀所需动作平衡力
闭阀后,导阀内部力的平衡方程式如下:
F1≥F2-F3

式中:F2——导阀关闭后其阀孔前的力,N;
F3——导阀关闭后其阀孔后的力,N;
P1——活塞上腔介质压力,Pa;
A1——导阀阀座孔截面积,m2。
3.1.4密封比压q的选择
密封比压的计算:
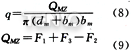
密封面的实际比压值q应满足下列关系:

式中:q——密封比压,Pa;
QMZ——导阀阀座密封面上的总作用力,N;
qMB——导阀密封面上的必须比压,Pa;
dm——导阀阀座密封面内径,m;
bm——导阀阀座密封面宽度,m;
[q]——许用密封比压,Pa。
3.1.5 双金属片组片数n的确定
联立式(7)、(8)、(9)和(10),得
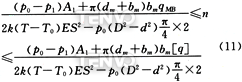
3.2先导阀口径的设计计算
双金属组件热动力元件作为超大排量疏水阀导阀的关键部件,其启闭速度决定着整台疏水阀的动作灵敏度。其灵敏度过高容易引起管路水击现象,从而引起管路异常振动甚至导致破坏;而其灵敏度过低则将增大疏水阀的漏汽率。可见,有效地控制双金属组件热动力元件的灵敏度,对疏水阀性能的稳定与提高具有重要的意义。为避免水击现象的发生,需要对先导阀的口径进行限制,以便控制主阀的开阀时间。
假设将先导阀安装在长为L的管路中,流体在管路中的流速为V。(过热蒸汽一般为40~60m/s),忽略活塞小孔的排液量可得:
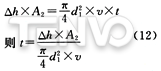
式中:△h——活塞行程,m;
A2——活塞顶部横截面积,m2;
d1——导阀直径,m;
Vs——管路中的流速,m/s;
ν——导阀阀座中冷凝水的流速,m/s;
t——主阀关闭时间,s。
根据水击原理当t》2L/Vs时不会引起水击,由以上分析可以得出导阀口径d1,满足
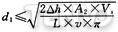
时不会发生水击。
4.主阀关键技术研究
4.1 主凋阀芯组件的受力分析
根据设计工况、主阀阀座和阀瓣密封副所需要的密封比压,对主阀阀芯组件进行受力分析可得(如图4所示):
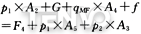
则活塞的顶部横截面积计算式为:

其中主阀密封面上的必需比压为:
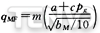
式中:G——主阀阀芯组件自身重力,N;
f——活塞环与气缸的摩擦力,N;
qMF——主阀密封比压力,106Pa;
A3——活塞底部横截面积(活塞的顶部横截面积减去阀杆的面积),m2;
A4——主阀密封面面积,10-6m2;
P2——活塞下部介质压力,Pa;
F4——主阀弹簧回复力,N;
A5——主阀介质作用面积,m2;
m——与流体性质有关的系数;
α,c——与密封面材料有关的系数;
pg——公称压力,106Pa;
bM——密封面宽度,10-3m。
由以上计算式,可根据设计工况通过反复计算来优化回复弹簧的受力,进而优化主阀阀芯组件的整体结构设计。
4.2 主阀回复弹簧的设计
主阀回复弹簧力的大小直接影响到疏水阀主阀的性能,力太大容易引起水击现象,力太小则会导致漏汽率增加,因此,对回复弹簧的设计相当必要。由4.1中的分析可知,主阀回复弹簧受到的力的大小为F4,另外,根据具体使用场合选定弹簧的材料,查表可得材料的许用应力[τ],然后按强度和刚度要求设计圆柱螺旋压缩弹簧。
首先,在弹簧的旋绕比C=4~8范围内初选,并由下式可得弹簧材料直径d2为:

式中:K——曲度系数。
根据计算值查得d2的系列值,再由弹簧中径D2=cd确定下D2。
弹簧的有效圈数可由下式计算:

式中:G2——弹簧材料的切变模量,109Pa;
f2:——弹簧变形量,10-3m;
k——弹簧刚度,103N/m;
kd——弹簧单圈刚度,103N/m。
由于C的不确定,可以根据不同的C值进行多组计算,比较计算结果,选取最佳方案,以便优化弹簧的受力。
4.3 主阀关闭时设计计算
主阀的关阀时间是反映整台疏水阀性能的重要指标之一,它与整台疏水阀的设计排量、漏汽率有着直接的关系。超大排量双金属可调先导式疏水阀主阀的关阀时间的长短与活塞上腔的体积、介质压力以及活塞小孔的大小有关,根据流体力学上的原理计算如下:
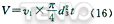
由伯努利方程可得:
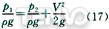
将式(16)代入式(17)可得:
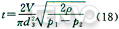
式中:V——活塞上腔体积,m3;
ν1——活塞小孔处液体流速,m/s;
d3——活塞小孔直径,m;
ρ——液体密度,Kg/m3;
t——关阀时间,s。
由式(18)即可确定主阀的关阀时间,结合水击原理,该时间应在满足t》2L/Vs的同时,还要保证整台疏水阀的漏气率满足要求。
5.结语
双金属可调先导超大排量蒸汽疏水阀是一类用于特殊场合的高参数蒸汽疏水阀,它采用的是热静力导阀+活塞主阀的设计,可用于有过冷度和过热蒸汽的场合,该产品的开发可为相关应用行业提高能源利用率、节约能源开支提供了保障。
目前国内主要存在问题在于:高温工况下国产双金属材料、弹簧材料性能的稳定性差,不能满足高于250℃的使用要求,与德、美、日等发达国家有很大距离。这就要求我们联合材料研究机构和生产企业,研发新材料,满足需求。
综合上述,该设计具有超大排量,可满足工业需求,节约能源。其研发思路还可为疏水阀、减压阀等自力式控制类阀门新产品的研发提供了一定参考。
蝶阀厂家-天沃,与您资料共享!