1.引言
随着减压阀在国内得到广泛应用,产品性能与寿命试验日益受到关注,在新型减压阀国产化配套设备研制过程中,应用计算机测控技术,设计国内首次自主研发的具有国际先进水平的减压阀动态性能与寿命试验的多功能高性能测试装置,为摸清实际产品性能、改进设计方案提供参考依据。
2.测试系统及其控制调节
减压阀动态性能测试系统如图1所示,以高压多级泵为压力源,被测阀前压力调节阀安装在回水旁路上。试验过程中,减压阀阀前、后压力都要调到额定值,阀前压力通过旁路调节阀调节,阀后压力调节应在阀后调节阀保持一定开度后再调节被测阀。
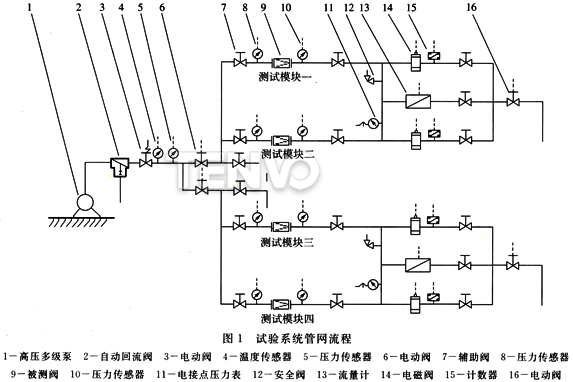
压力流量等常规性能试验是检验减压阀产品合格与否的重要依据,为考核膜片、弹簧等元件还需进行产品寿命试验,才能为进一步提高和改善产品的可靠性和安全性提供全面的依据,为实现这一目的首先要解决试验系统恒流量下的压力控制问题,即一方面阀的进口压力要调节到试验工况所需压力值;另一方面要在恒流量下使阀的出口压力也能够调节到试验工况所需压力,而为了保证试验过程的稳定性,必须保证连续的恒压供给;同时为满足不同产品的试验要求,试验系统还需实现对流量及阀前后压力的自动控制与调节,才能满足多工况运行与各类试验要求。由于用户需求测试产品包括PNl.6~4.O、DN25~300共数十个规格,测试系统采用图2所示的模块化设计。用电磁阀模拟实际系统调节频率进行寿命试验时,因电磁阀局部阻力大,影响其他试验项目的流量调节范围,故各模块又分两路,分别进行流量特性、压力特性、流阻特性、流量系数和寿命试验。为保证高压泵和系统安全运行,设置了集流量感知、止回、旁通控制、多级降压多功能于一体的LYHT型自动回流阀,省却了单独的孔板、流量计、电磁控制旁通控制阀,简化了旁通回流系统,维持高压泵最小回流,当系统出现故障或调整试验项目时,自动回流阀主阀关闭,旁通阀开启,泵以小流量回流避免频繁启动,更经济有效地保证系统安全运行。阀前后与阀前旁路均采用高精度自动调节阀,实现了阀前后压力和流量调节与稳定控制。
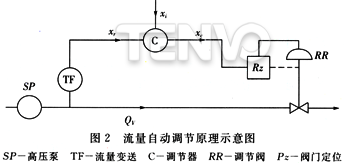
图2为流量自动调节原理示意图,高压泵输出流量为Qv,由流量变送器TF测量并输出信号xr传给调节器C;给定信号xi是一个常数,由操作人员给定;调节器发出控制信号xc通过阀门定位器Pz作用在调节阀上。如流量下降,调节器C将调节阀开大,直到恢复到原定流量,当流量增加时,调节器将调节阀关小。图3为泵与管网特性曲线,设高压泵转速恒定,工作点为管阻与泵特性曲线的交点(Qvo,P0)。当管路损失增加时,管路特性由曲线2变为曲线3,流量降为Qv1。为使流量恢复Qvo,需使调节阀开度增大,以减小管路损失,使管路特性曲线恢复至曲线2,流量Qv1重新恢复到给定值Qvo。反之当管路损失降低时,曲线偏移为4,自动调节系统将调节阀关小,使流量Qv2恢复到Qvo。
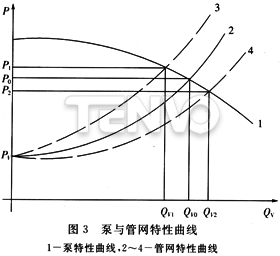
图4为阀前压力自动调节示意图,图6为泵与主旁管路及整个管网系统特性曲线,假设给定某稳定工况点(P0、Qvo),此时被测阀阀前和旁路调节阀阀前压力P1近似等于泵出口压力P0高压泵总流量为主管流量Qvc和旁路流量Qvb之和。试验过程中被测阀阀前后压力也都需要调节为试验规定值。被测阀阀前压力首先通过阀前旁路调节阀进行调节,然后通过被测阀及其阀后调节阀后压力,如被测阀前压力产生波动,再重复上述过程,直至使被测阀前后压力逐步趋于试验所规定的额定值。
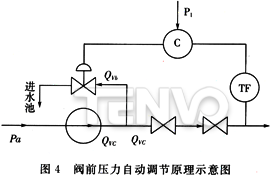
如图5所示,假设为了增大被测阀前后压差,操作人员需要关小其开度,而此时主管阻力曲线将从2变为2′,而整个管网系统的阻力曲线随之由3改变到3′,这时高压泵出口压力由P0增加到P01,阀前压力随之增大,则压力变送器测得的被测阀门前压力与给定值产生一个偏差,调节器C会控制旁管路调节阀开大,使旁路阻力变小,其阻力曲线由1变成1′,流量变为Qvb1,直至整个管网阻力曲线由3′返回3,使高压泵出口压力又趋于P0直至被测阀前后压差增加至试验所需要的规定值。反之为减小被测阀前后压差,其原理与上述类似,但调节过程正好相反。
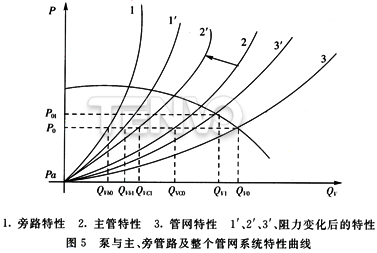
3.测试项目与试验结果
根据用户要求所需进行的减压阀动态运行特性试验包括“流阻——流量特性”试验、“流量特性”试验、“压力特性”试验、“流量系数”试验及寿命(连续运行特性)试验等。
3.1“流阻——流量特性”试验
流阻特性试验:保持被测阀门进口压力不变,调节被测阀门的调节弹簧,得到不同的出口压力和流量,找出流量和压差的关系,并做出△P—Q曲线。
图6~图9中以Y43H—40 DNl00被测阀为例,分别保持某一阀前进口压力(P1=4.0MPa、P1=3.0MPa、P1=2.5MPa、P1=1.6MPa)不变时的“流阻——流量特性”曲线图。
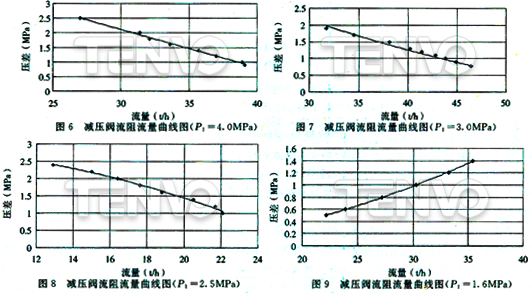
3.2 “流量特性”试验
给定被测阀前最高允许工作压力,调节被测阀后为某一出口压力,测定该工况下的流量值,然后调节流量至该工况的20%,测定两种工况下的出口压力偏差值△P1/P2。根据GB/T12245减压阀试验方法的要求|△P2/P2|平均值≤10%,考核流量变化时的阀后稳压能力,试验数据见表1。
P2/MPa | P1/MPa | Q/M3·h-1 | 0.2Q/M3·h-1 | P″2/MPa-1 | P″2-P′2/P′2 | ||
额定P2 | 实测P′2 | 实测 | 实测 | 额定 | 实测 | 实测 | |
1.00 | 0.99 | 3.00 | 35.29 | 7.06 | 7.01 | 1.15 | 16.16% |
1.20 | 1.20 | 3.01 | 39.00 | 7.80 | 7.77 | 1.19 | -0.83% |
1.40 | 1.41 | 3.00 | 40.57 | 8.11 | 8.21 | 1.39 | -1.42% |
1.60 | 1.58 | 3.03 | 42.57 | 8.51 | 8.41 | 1.60 | 1.27% |
1.80 | 1.80 | 3.02 | 47.87 | 9.57 | 9.66 | 1.75 | -2.78% |
3.3 “压力特性”试验
给定被测阀前最高工作压力,调节被测阀为某一出口压力,测得该工况下流量值,保持流量不变,使进口压力在80%~105%最高工作压力范围内变化,测定此时出口压力偏差值△P2/P2根据GB/T12245要求|△P2/P2|平均值≤5%,考核进口压力变化时的阀后稳压能力,试验数据见表2。
P1 | 0.8P1 | 0.85P1 | 0.9P1 | 0.95P1 | 1.05P1 | |
额定P1/MPa | 1.6 | 1.28 | 1.36 | 1.44 | 1.52 | 1.68 |
额定P′1/MPa | 1.6 | 1.28 | 1.36 | 1.44 | 1.51 | 1.68 |
p2/MPa | 0.40 | 0.40 | 0.40 | 0.40 | 0.40 | 0.40 |
p′2/MPa | 0.40 | 0.41 | 0.41 | 0.40 | 0.40 | 0.37 |
(p′2-p2)/p2 | 0 | 2.5% | 2.5% | 0 | 0 | -7.5% |
Q/M3·h-1 | 8.81 | 8.81 | 8.81 | 8.81 | 8.81 | 8.81 |
Q′/M3·h-1 | 8.81 | 8.86 | 8.84 | 8.84 | 8.84 | 8.83 |
3.4 “流量系数”测量
流量系数:是衡量流通能力的指标,流量系数值随被测阀的尺寸、形式、结构而变化,目前先进工业国家已对减压阀流量系数有比较深入的研究,而国内尚比较缺乏对这此类产品深入的试验与研究,表3为Y43H—40型减压阀的流量系数试验数据。
进口压力P1/MPa | 进出口压差△P/MPa | 出口压力P2/MPa | 流量Q/M3·h-1 | Cv |
3.05 | 0.10 | 2.95 | 18.51 | 21.60 |
3.02 | 0.10 | 2.92 | 18.41 | 21.48 |
3.03 | 0.10 | 2.93 | 17.71 | 20.70 |
Cv平均值 | 21.26 |
3.5 “连续运行特性”试验
寿命(连续运行特性)试验以某一频率连续启闭,考核弹簧、膜片磨损与寿命,每次启闭为一试验循环,单位时间动作次数为频率。试验循环次数与动作频率应参照GB/T12245,表4中试验次数按规定为5000次。
进口压力P1/MPa | 出口压力P2/MPa | 进出口压差△P/MPa | 电磁阀启闭n/次 | 弹簧膜片状况 |
2.50 | 1.00 | 1.50 | 0 | 良好 |
2.27 | 1.00 | 1.27 | 2500 | 良好 |
2.47 | 1.00 | 1.47 | 4000 | 良好 |
2.17 | 1.00 | 1.17 | 4500 | 良好 |
2.41 | 1.00 | 1.41 | 5000 | 良好 |
4.试验数据分析
为评定试验精度需要对试验数据进行误差分析,限于篇幅本文仅以流阻试验为例进行试验误差分析。设试验过程中需要测试的一个工况点为:阀前压力P1=4.OMPa,阀前后压差△P=2.0MPa,表5所示为间隔一分钟读数所得到的十组试验数据。
阀前压力(MPa) | 阀前后压差(MPa) | 流量(M3/h) | 测试时间 |
4.06 | 1.98 | 21.79 | 10:05 |
4.03 | 1.96 | 21.82 | 10:06 |
3.95 | 1.97 | 21.86 | 10:07 |
3.98 | 2.01 | 21.85 | 10:08 |
4.00 | 2.02 | 21.75 | 10:09 |
4.02 | 2.00 | 21.76 | 10:10 |
4.04 | 1.99 | 21.77 | 10:11 |
3.99 | 1.99 | 21.82 | 10:12 |
4.06 | 1.97 | 21.76 | 10:13 |
4.04 | 2.03 | 21.78 | 10:14 |
4.1 随机误差
首先计算10个流量值的平均值:(3)
将表5中的数据代入式(3)得:
计算其偏差值的平方和:(4)
将表5中的数据代入式(4)得:
计算测量值的均方根误差和极限误差:(5)
(6)
将数据分别代入式(5)、(6)得到:
同时检查Vi的值,如其中有大于△lim者,应将该测量值剔除,再重复上述步骤。
计算算术平均值的均方根误差及其极限误差:(7)
(8)
将数据分别代入式(7)、(8)得到:
计算算术平均值的相对极限误差:(9)
将数据代入式(9)得到:
4.2 系统误差
(1)根据系统配置的流量测试仪表精度等级得到:δy=±0.5%
(2)温度变化引起的测量误差:
试验过程中由于水的密度随水温有所变化,将带来流量测量误差。设最大温升为5℃(如温度由28℃升高到33℃),查水的物性表知:在一个大气压下,密度由996.23Kg/m3。变为994.70Kg/m3,变化率为±0.1%,也就是说由于温度升高给流量带来的测量误差为δt=±0.1%。
(3)水泵的非稳定运行引起的测量误差:
试验过程中由于电网波动,水泵的扬程和流量产生波动所带来流量测量误差:δp=±0.1%。(计算过程略)
4.3 测试误差
由上述随机误差和系统误差,得到总测量误差为:δ=±(1.5+0.5+0.1+0.1)%=±2.2%。
同理可计算得出阀前压力、阀前后压差的测量误差分别为±2.1%和±2.3%。
5.结论
厂所合作研制减压阀动态性能与寿命试验装置经专家技术鉴定和使用效果证明,系统测试范围宽、功能全、运行稳定,测试项目及精度等均达到GB/12246—2006的要求,填补了国内目前提出测试要求而无实测条件的空白。
天沃-电动调节阀门,与您资料共享!